Warehouses are where the rubber meets the road in any supply chain – but they can also be a significant source of costly errors. Human error remains a consistent obstacle for warehouses, with 46% suffering from it as the primary cause of the goods-in disruption. Human mistakes account for many problems, ranging from inventory discrepancies to shipment issues.
Fortunately, you can take proactive steps, like Warehouse Management System, to minimise these risks and streamline your warehouse’s processes. The steps also include better training regimens and enhanced technological automation solutions. In this article, we’ll investigate more such strategies!
What Is Warehouse Management
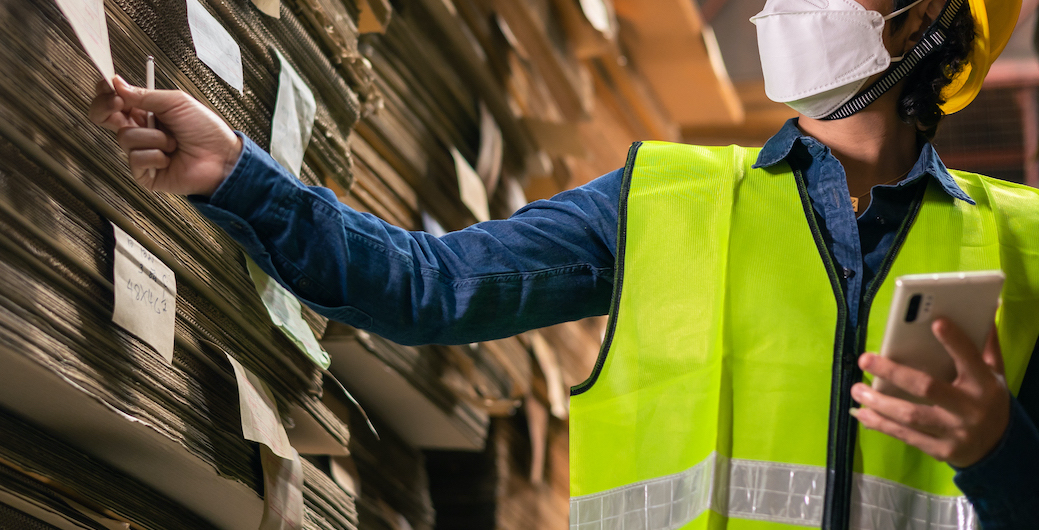
Warehouse management refers to the process of overseeing and controlling the operations of a warehouse. This includes everything from receiving and storing inventory and fulfilling orders to maintaining the organisation of the warehouse.
Tasks such as inventory management, space optimisation, and visitor monitoring define warehouse management. It is an integral element of supply chain management, which helps ensure that products are stored and distributed efficiently. It ultimately aids in reducing costs and improving customer satisfaction.
Challenges in Warehouse Management
A staggering 90 fatalities and 34,900 serious injuries occur annually due to forklift-related accidents. It is a grim reminder of manual warehouse management’s dangers. Several other challenges can arise in warehouse management, mainly when relying on manual processes and human labour. Some of these challenges include
- Human error: Manual processes can lead to costly mistakes, such as mislabeling or incorrectly locating merchandise. This increases the chances of inaccuracies in inventory and delays order processing times.
- Inefficiency: Manual processes can drastically drag down productivity, leading to hours of wasted effort, time, and costs for businesses.
- Lack of visibility: With real-time data and accurate inventory tracking, it can be easier to know where items are located within the warehouse. This can lead to delays in fulfilling orders.
- Safety risks: Without properly addressing manual processes, such as lifting and handling heavy items, increased workplace injuries may become an unfortunate reality.
- Limited scalability: As a business grows, manual processes may become increasingly difficult to manage, limiting the ability to scale operations.
Many companies are turning to technology solutions such as warehouse management systems (WMS) and automation to overcome these challenges.
Tips For Reducing Human Errors In Warehouse Management
Here are some tips for reducing human errors in warehouse management:
Implement a Real-Time Inventory/Warehouse Management System
Human error can significantly impact warehouse operations and lead to costly delays. Though, these can be reduced by implementing a real-time inventory/warehouse management system. The WMS already knows an item’s inventory before creating the picking wave and automatically generates the most efficient picking route.
This eliminates guesswork and leads to improved accuracy throughout the process. Additionally, visual cues such as colour coding and barcodes help operators pick the correct SKU (Stock Keeping Unit). Furthermore, cloud-based automated sortation solutions provide ultra-high sorting accuracy of 99.99%, far much higher than manual sorting. This ensures that orders make it to their destinations on time and hassle-free.
Invest in Employee Training
It is crucial to invest in employee training so that everyone understands the warehouse management system and its proper use. This can help reduce the risk of human error. Empowering staff with automation and training them for it can also affect their productivity. You can fulfil your promise for the end-customer without delays.
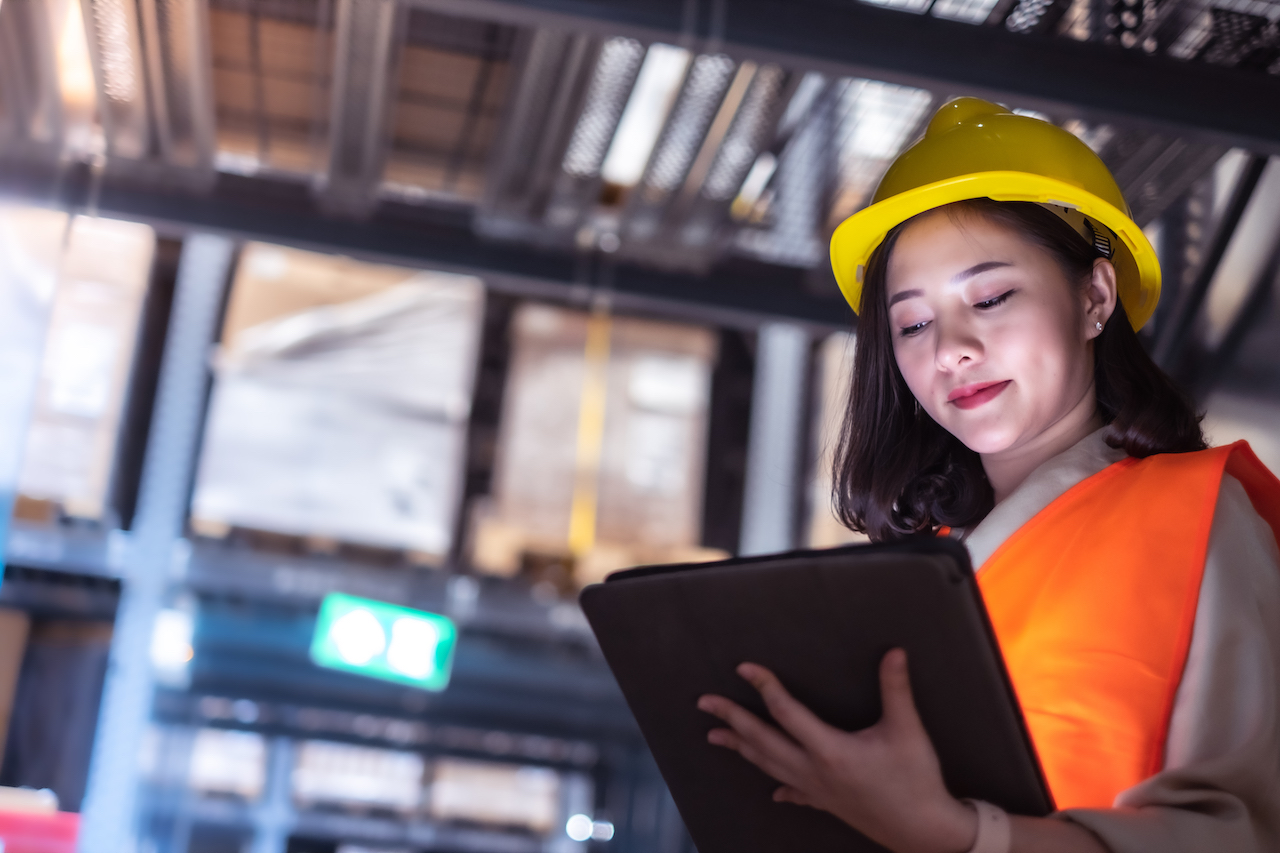
Regularly Audit And Review
The importance of regular audits in warehouse management is paramount. By periodically evaluating inventory levels, supplies and processes, managers can reduce human errors associated with oversight. This comes into play by improving accuracy and avoiding costly mistakes that could create problems further down the supply chain. Moreover, scheduled performance reviews offer insight into where improvements may be necessary to ensure efficiencies – such as process edits or personnel changes.
Mapping End-to-End Processes And Increasing Accountability
Mapping out end-to-end processes and increasing accountability is vital for a clear overview of the life cycle of each step. That way, you will have a more accurate view of what tasks are currently taking place and when throughout the process. With well-defined roles for each employee, it ensures everyone understands their duties and responsibilities, making them more accountable.
Review Storage Strategies Regularly
Proactively examining storage systems can be an effective way of pinpointing potential problems and avoiding unwelcome surprises. Doing so optimises costs and bolsters customer relations through more efficient product distribution.
Conclusion
In conclusion, human errors can significantly impact the efficiency and accuracy of warehouse operations. Implementing a real-time inventory/warehouse management system, investing in employee training, mapping end-to-end processes, increasing accountability, and empowering staff with automation tools can also help improve warehouse management and reduce the risk of errors. These steps help you improve your warehouse operations’ overall efficiency and accuracy, which can help reduce costs and improve customer satisfaction.