Logistics is a complicated yet necessary business. From farming to military peacekeeping operations, almost all activities rely on the essential resources becoming available at the appropriate time. However, even the most prominent corporations often leave out the last-mile delivery’s final and most essential component. Throughout this guide, we’ll understand the various issues SMBs and big firms face and how automation methods can mitigate them.
Why Does the World Need Automation of the Final Mile?
The last mile of any supply chain involves the goods being finally delivered to the customer or organisation expecting them. While it only consumes about 20% of the delivery time, starting from packaging, the final phase constitutes 53% of the total shipping cost.
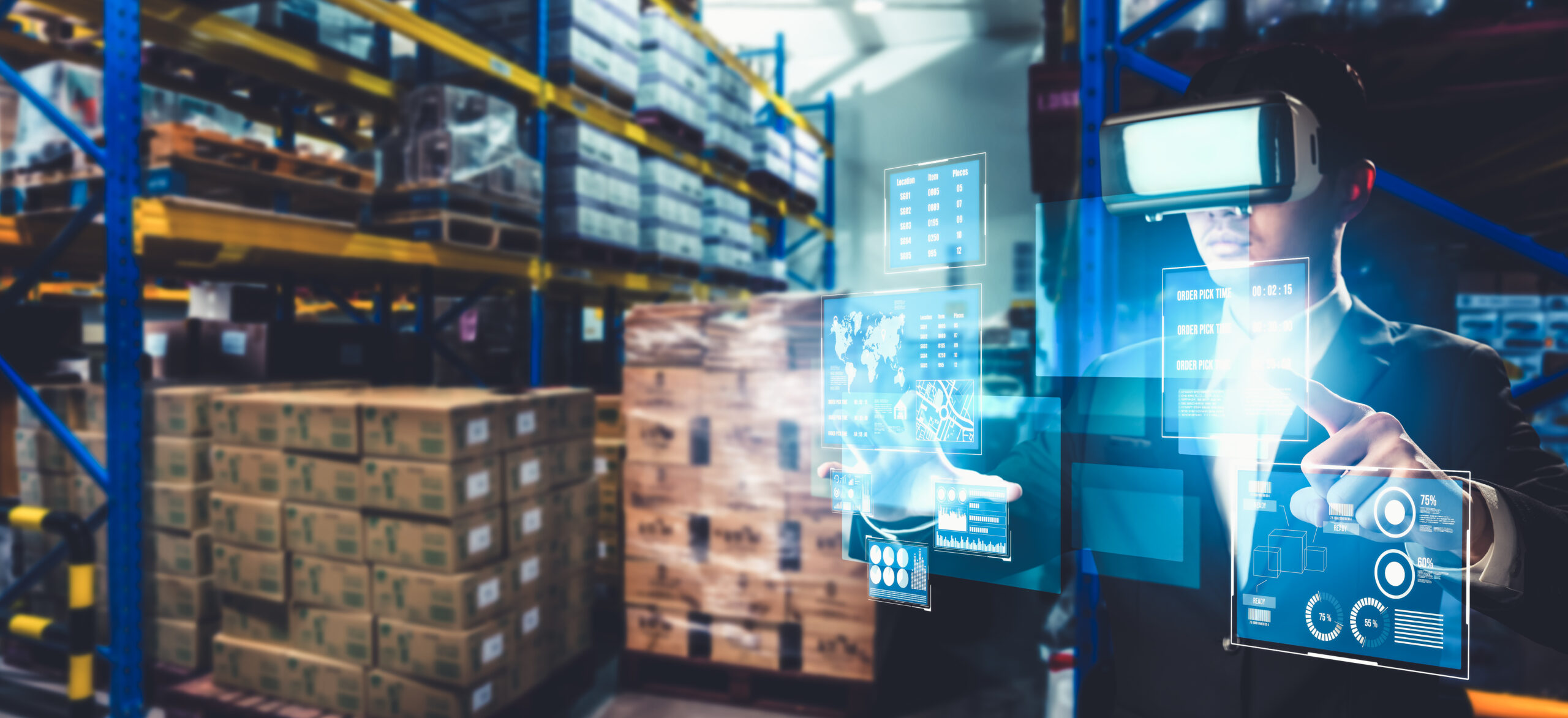
Businesses of all shapes and sizes are implementing the Internet of Things (IoT) to automate monitoring in warehouse operations, RFID chips for automated shipment tracking, and sophisticated new warehouse management systems (WMS) for reducing manual effort. Yet, all of that amounts to nothing if the last mile of the delivery isn’t efficient.
You can also encounter issues affecting your business’s bottom line in a few areas.
1. Routing and Dispatching
The last-mile navigation can present random events to hamper the delivery of any package up to that point. A snowstorm blocking traffic or a road closure can occur due to unforeseen construction. Moreover, there are often problems planning the most efficient dispatch, as deliveries with fewer customers can be completed quickly, leaving vehicles unrouted for more urgent parcels.
2. Customer Communication
It takes work to update the customer through conventional means, such as texts and emails, during the last mile of the delivery. It requires minute-by-minute updates that can get annoying for both the supplier and the receiver.
3. Invoices and Driver Settlements
It’s challenging to manage the scale of success each driver achieves throughout their day. A few can put in extra miles to ensure deliveries, while others can slack off with fewer deliveries. Thus, analysing their payouts is tough, so deserving drivers often feel left out, resulting in massive turnovers.
What Kind of Automation Methods of the Final Mile Provide for These Issues?
Final mile automation methods can minimise those issues through the following means.
SaaS AMS and WMS
Integrations for smart automation, such as IoT, can allow last-mile drivers to remain connected with the fleet and customers. Digital Asset Tracking Systems (AMS) and WMS can enable managers to monitor the condition of their fleets closely and plan accurate routes before dispatching drivers.
Apps For Regular Updates and Emergencies
An app for both the last mile employees and the customers can automate the updates upon request. It allows for precise delivery times so that the first attempt is successful while also allowing drivers to raise emergency tickets in case of blockades or accidents.
Saving Paper Through Digital Technology
Digital automation methods can make the last mile process free of any paperwork. The customer can give their digital signature, while the driver can notice the invoice updated within minutes of delivery.
Advanced Logistics Simulations
Automation methods involving AI and ML can assist with testing the business model for various companies without any practical risks. They can highlight the problems that require addressing so that the model can be modified for optimal performance.
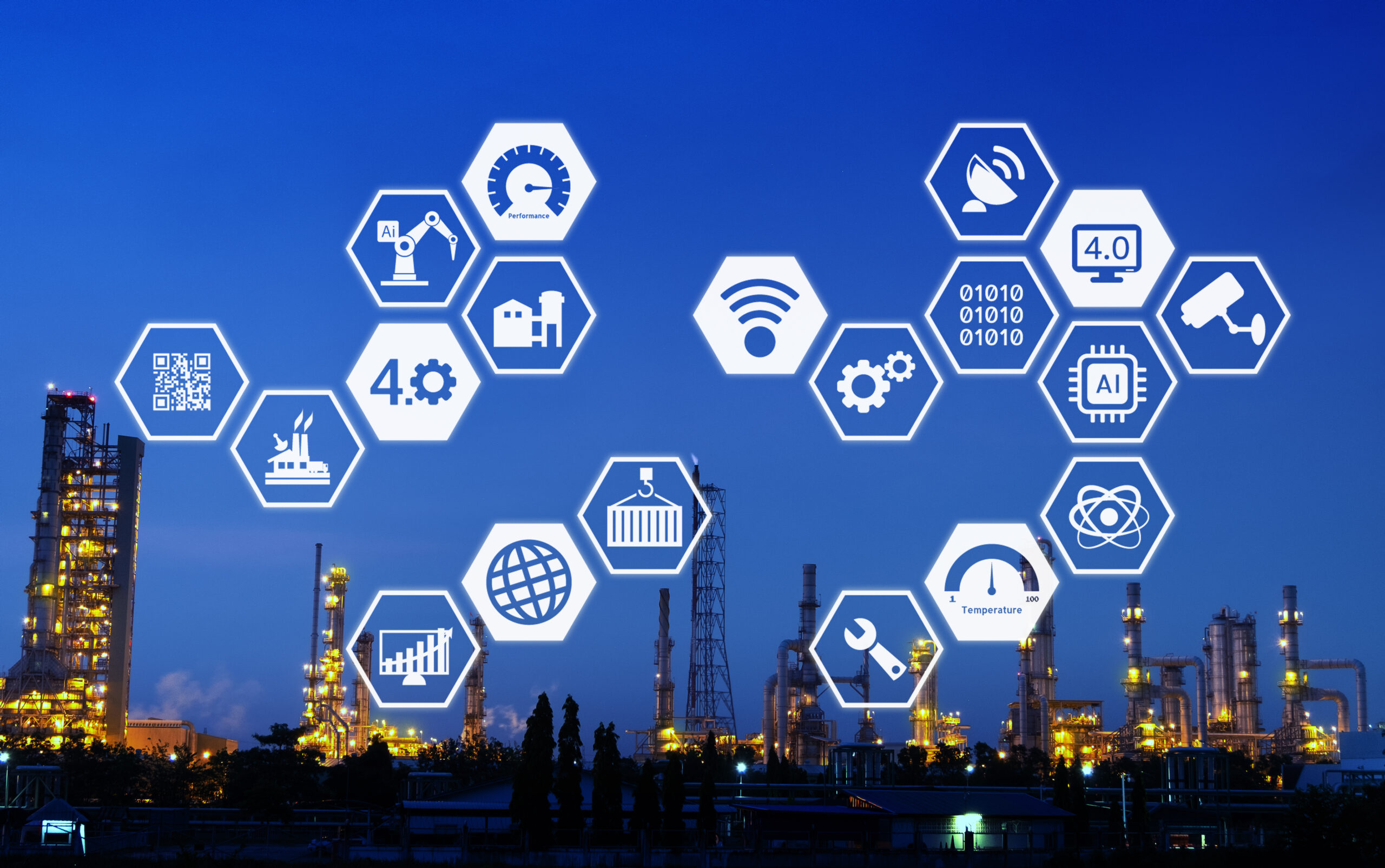
Your enterprise can reap the following advantages from last-mile automation.
- Reduce Human Error: Introducing software for last-mile deliveries can seem an obstacle. Yet, it can reduce human error and the likelihood of an order being returned or refunded.
- Appropriate Customer Feedback: With automation, you can obtain precise feedback from the customer, so you can investigate the precise issue of dissatisfaction and remedy it for future orders.
- Lower Fuel Consumption: Last-mile automation lets drivers remain efficient while driving instead of idling their vehicles as they try to locate the following address. You can also introduce EVs in your fleet.
- Increased Safety Without Compromising Speed: Automation methods often ship with a platform with the tools to measure the safety parameters of each delivery. Your facility manager can ensure all employees follow protocol instead of checking the CCTV recordings for 8-hour shifts.
Short Summary
The last-mile delivery operations decide your company’s future since this part of the delivery has many challenges. Fortunately, you can overcome them and grow your business by utilising the right technology. Still, it depends upon the service provider of your choosing. For the best automation methods for your warehouse or fleet systems, check out Qbasis today.