Maintenance management plays a vital role in maximising the equipment lifespan within organisations. Effective maintenance practices ensure that equipment functions optimally, minimising downtime, reducing costs, and prolonging operational life.
The importance of maintenance management in maximising equipment lifespan highlights the significance of proactive maintenance strategies, regular inspections, timely repairs, and the utilisation of advanced systems.
Organisations prioritising maintenance management can enhance operational efficiency, improve asset reliability, and achieve long-term cost savings.
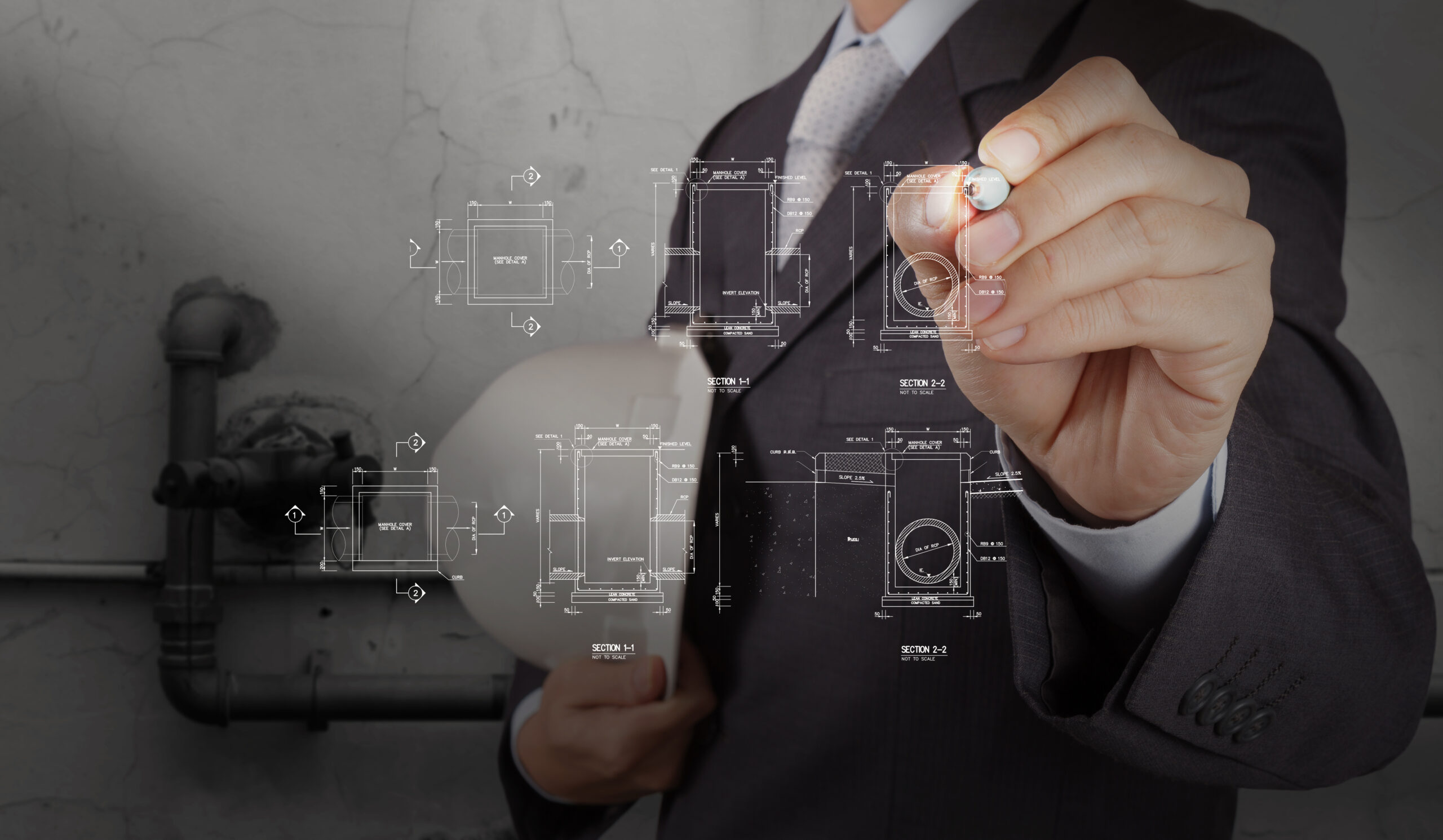
Maintenance management for assets
Maintenance management for assets involves effectively planning, coordinating, and controlling maintenance activities to ensure physical assets’ optimal performance and lifespan.
This process often relies on maintenance management software, such as Computerised Maintenance Management System (CMMS), to streamline and automate various maintenance tasks.
CMMS software is a powerful tool that enables organisations to manage their maintenance operations efficiently. It provides a centralised platform to store and access important information related to assets, maintenance schedules, work orders, inventory, etc. CMMS software enables maintenance teams to track and manage maintenance activities, allocate resources, and monitor asset performance.
One of the critical features of CMMS software is scheduling preventive maintenance tasks. Preventive maintenance involves regularly scheduled inspections, servicing, and repairs to detect and address potential issues before they become costly breakdowns.
With CMMS software, maintenance managers can create maintenance schedules, set up automated reminders, and generate work orders for preventive maintenance tasks.
CMMS software also facilities maintenance management. When unexpected equipment failures or breakdowns occur, maintenance teams can quickly generate work orders, assign tasks, and track the progress of repairs using the software. It helps minimise downtime and ensures that repairs are conducted promptly.
Also, CMMS software enables organisations to manage their inventory and spare parts efficiently. Maintenance managers can track inventory levels, monitor usage, and generate purchase orders when stock levels are low. It ensures that the necessary parts and materials are readily available for maintenance and repairs, reducing equipment downtime.
Implementing CMMS Software for Maintenance Management
Maintenance management is critical in ensuring the optimal performance and longevity of assets.
Organisations often use asset maintenance management software, such as Computerised Maintenance Management Systems (CMMS), to streamline and improve maintenance operations.
Let us discuss the process of implementing CMMS software and its benefits in maintenance management. We will focus on selecting the right software, configuring and customising it for specific needs, and integrating it with existing systems and workflows.
Selecting the Right CMMS Software for Specific Needs
The first step in implementing CMMS software is selecting the right solution that aligns with the specific needs and requirements of the organisation. Various CMMS software options are available, each with its features and functionalities.
Evaluating and comparing different software packages is crucial based on ease of use, scalability, reporting capabilities, mobile accessibility, and integration capabilities.
Organisations should consider their maintenance management goals, the size and complexity of their asset portfolio, the number of users, and any specific industry or regulatory requirements.
Organisations can make an informed decision when choosing a CMMS software solution by conducting thorough research, requesting demonstrations, and seeking recommendations.
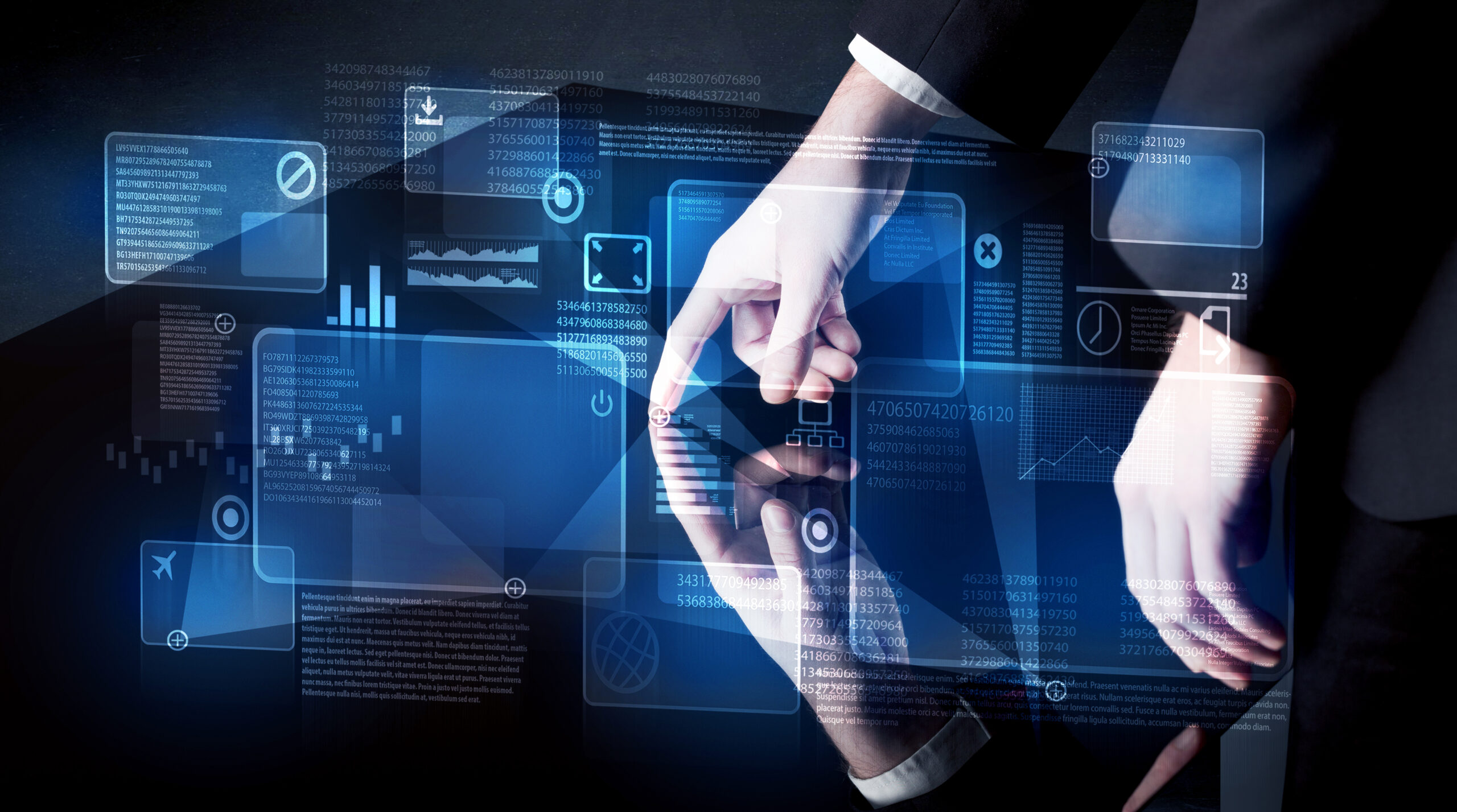
Configuring and Customising CMMS for Effective Maintenance Management
Once the appropriate CMMS software is selected, the next step is configuring and customising the software to meet the organisation’s unique maintenance management needs.
It involves setting up user roles and permissions, defining asset hierarchies and categories, creating preventive maintenance schedules, and configuring workflows and notifications.
Organisations should align the CMMS software with their existing maintenance practices and standard operating procedures during the configuration process.
It ensures a smooth transition and enables employees to adapt quickly to the new system. Additionally, customisation options should be explored to tailor the CMMS software to specific requirements, such as adding custom fields or integrating with industry-specific tools or regulations.
Integrating CMMS with Existing Systems and Workflows
It is crucial to integrate CMMS with existing systems and workflows. CMMS software can seamlessly integrate with other software applications, such as enterprise resource planning (ERP), procurement, or financial systems, to enable data sharing and streamline processes.
Integration wipes off the need for duplicate data entry and enables real-time information exchange between systems. For example, integrating CMMS with an ERP system allows maintenance teams to track inventory levels, generate purchase orders, and manage the financial aspects of maintenance seamlessly.
Also, integrating CMMS software with mobile devices, sensors, or Internet of Things (IoT) devices can enhance data collection and facilitate remote monitoring of assets. It enables maintenance teams to receive real-time alerts, access work orders, and update asset information directly from the field, improving response times and efficiency.
Summary
Maintenance management maximises equipment lifespan and ensures assets’ long-term performance and reliability. Organisations can significantly extend the lifespan of their equipment, minimise downtime, and reduce overall maintenance costs.
It involves various practices, including preventive, predictive, and reactive maintenance, aiming to proactively identify and address potential issues.